APH-5 helmets
Latest update 14 January 2007Description
of APH-5 helmet from NAVPERS 10358-A, Parachute Rigger 3 & 2 from
around 1960
Article from Naval Aviation News, June
1956
Article from Approach, January 1957
Group discussions
Development
The APH-5 helmet was the result of more than two years studies conducted 1954-56 for a
successor to the H-3 and H-4 series of helmets. VX-3 at NAS Atlantic City, the Aero
Medical Branch of Service Test Division at NATC Patuxent River, Air Crew Equipment
Laboratory, Naval Air Materiel Center, Philadelphia, and AirLant and AirPac Fleet units
were among those who coorporated with the Airborne Equipment Division of BuAer in testing
the gear. The studies and helmet development work included with the MSA-N2 design, an
immediate predecessor of the APH-5, being manufactured in very limited quantity. Another
contract initiated work on an individually fitted (custom fit) helmets, designated the BBC
and BBC-X2.
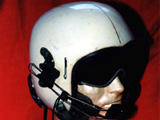 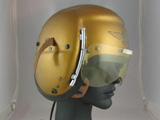 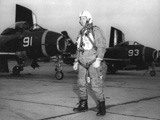 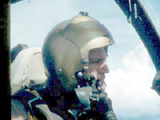
Far left: Although unconfirmed, this helmet
is thought to be the BBC-X2; one of the designs studied in the process
that lead to the APH-5 helmet. It is characteristic by having a visor that retracts inside
the helmet shell, much like
the visor design used the the French company Gueneau later on. Left: This
DH-5-3 helmet was Gentex' bid for a
successor to the H-4 helmet but it was a MSA design, the APH-5, that won the competition. Right:
A pilot at Naval
Air Materiel Centre wearing an APH-5 prototype helmet. This picture was taken as early as
26 October 1954, docu-
menting the long development process that lead to the service introduction of the helmet
18 months later. Far
right: A 1957 picture showing a pilot on a multi-engine aircraft wearing an
APH-5. This was very early since the
stated policy was to equip fighter and attack squadrons first. Pictures © Bloodhound,
Gentex, US Navy and unknown.
Production and entry into service
Initially, the APH-5 was designed without a visor, and the incorporation of a visor
required a cover plate in order that the helmet shell itself would not be weakened by the
visor guide slot. The final version was field tested for nearly a year by squadron pilots,
during which time some 50 helmets had an average of 300 flight hours logged. From the
comments and suggestions thus obtained, several modifications were made and the helmet was
put into production.
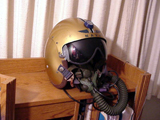 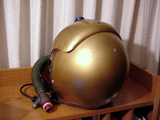 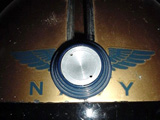 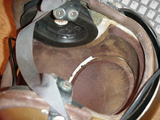
Far left and Left: Early
APH-5 helmet with an A-13A oxygen mask attached with Y-yoke. Right:
Close-up of the
stepped lock knob typical to some early APH-5 helmets. Far right: The
original sponge rubber lining which caused
heat build-up and collected perspiration. Pictures © unknown and Alan Masengale (lock
knob close-up).
The distribution of the APH-5 helmets began in April
1956, the first going to fleet squadrons as allocated by ComAirLant and ComAirPac. The
first two contracts (2500 under first contract, 2500 under second contract for 7500) had
been delivered by February 1957 allowing the helmet to become standard equipment in all
fighter and attack squadrons as originally intended. As the years passed and more helmet
became available they were issued to flying personnel from other squadrons as well.
Shortcomings
The APH-5 design was ground-breaking and set the standards for the vast majority of US
flight helmets until the advent of the HGU-55 in the early 1980s. It did however suffer
from a number of shortcomings, some more serious than others. From the beginning the APH-5
was suffering from heat built-up. The close fitting sponge rubber lining produced more
heat than the old cross-strap webbing of the H-3 and H-4. An associated problem was that
the sponge rubber collected perspiration in an unsatisfactory manner. Improved,
leather-covered liner pads were therefore introduced. Another frequent complaint about the
early helmets was that the visor lock button have been received -the binding problem was
solved in later models by the use of a template for aligning the track before riveting,
and by burnishing the visor track to reduce friction. The first 1500 helmets manufactured
had a plastic female communications plug on the left side of the helmet. It turned out
that it was poorly placed and subject to frequent breakage so later models had a lead-in
extending from beneath the edge of the helmet.
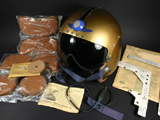 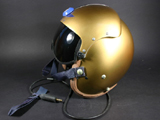 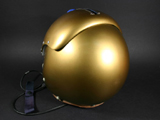 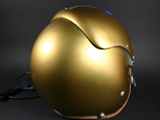
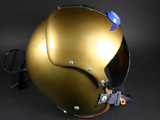 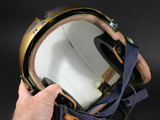 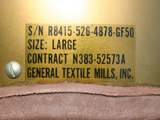 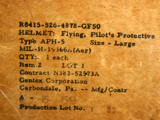
A wonderful series of pictures showing a factory-fresh APH-5
helmet made by General Textile Mills (later Gentex).
The upper, far left picture shows all contents of the original shipping box with fitting
pads, measuring tool and user
instructions. The lower, far right picture shows the print on the shipping box, telling us
that the helmet was manu-
factured in May 1959. Pictures © J.
Miller / Vintage Wings
Poor helmet retention
Poor helmet retention was the APH-5's most serious problem by far. In a time period of 12
months in 1958-59 there was a total of 52 cases of APH-5 loss during aircraft accidents in
the US Navy. Of these 52 cases, 50 percent were fatal while an additional 23 percent had
head injuries. Comparable figures for 1963 show 23 cases of APH-5 loss, with 48 percent
fatal injuries and 26 percent non-fatal head injury. Retention in the APH-5 was
accomplished by a nylon chin strap, nylon nape strap, three sizing pads of leather covered
foam rubber situated in the front, top and rear, and by ear pads of foam rubber attached
to polystyrene earcups.
The foam rubber composition of the sizing pads permitted
very small loads to compress the pads completely. In case of compression of the front
sizing pad, the nape strap lost contact with the head and became completely useless. In
case of compression of the top pad the slack created in the chin strap made it
ineffective.
Both the chin strap attached to the outside of the helmet and the napestrap had very
limited skin contact and therefore very little retention capability, even before sizing
pad compression, even if the straps were tightened to the point of intolerance for
prolonged wear.
The earcups were attached with a screw through the helmet shell, but the screw was only
fixed to the polystyrene earcup by a small fixture embedded in the foam. Even a small
impact would fracture the polystyrene earpad; and when this occurred, most of the
retention capability of the helmet was destroyed. Even if the polystyrene material
remained intact, the soft foam rubber earpads were compressed very easily, impairing the
retention capability.
Comfort
The APH-5 helmet was heavy and therefore uncomfortable to wear for longer
periods. It weighed 4 pounds with Hardman receivers but without oxygen mask. In comparison
an APH-6 helmet weihed only 3 punds 13 ounces. Some of the factors affecting the weight
were the heavy rubber edge beading, large earphones, and fibreglass visor housing. Other
factors adversely affecting comfort were problems with heat retention (even with the newer
fitting pads), abrasive chin and nape straps, and difficult fitting due to only two helmet
sizes available.
Oxygen mask attachment
The APH-5 went through several upgrades in order to improve oxygen mask
retention. Originally the helmet was issued with leather oxygen mask tabs with two male
studs on each, and the A-13A oxygen mask was attached using a Y-shaped metal yoke with
webbing straps. It quickly proved to be inadequate so the Hardman retention system, or
"Christmas tree" oxygen clip, were evaluated in 1957 and approved for use. The
oxygen mask clip could be quickly inserted in a slot receptacle on either side of the
helmet for a comfortable fit and a quick disconnection. Another step was taken when the
Navy adopted the self-aligning Sierra type 345-30 oxygen mask receivers by 1961. The
system retained the Hardman hardshell but introduced a new type of T-shaped bayonets,
easier to insert and release.
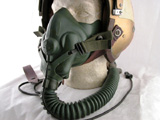 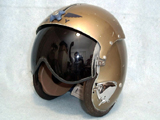 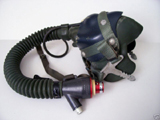 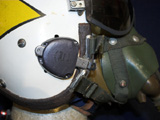
Far left: The original oxygen mask
attachment with the Y-shaped yoke, and webbing straps fastened with studs
to leather oxygen mask tabs. Left: APH-5 helmet with Hardman oxygen mask
receivers. Right: A-13A oxygen mask
with Hardman hardshell and the so-called Christmas tree bayonets that match the Hardman
receivers. Far right:
APH-5 with Sierra type 345-30 self-adjusting receivers and T-bayonets. Pictures ©
Chameloon, Shark, t5i6m60 and
Jukka 'JJ' Juutilainen.
Despite all the problems and shortcomings mentioned
above, the APH-5 was used extensively throughout the 1960s even if its successor, the
APH-6, was fielded around 1961. The APH-5 was modified with new fitting pads, new oxygen
mask attachment systems, the chin strap was moved inside the helmet shell, and both chin
and nape straps were fitted with cotton covered urethane pads for improved comfort. Some
APH-5s were even modified with APH-6 type headsets with the well-known external disc.
|